年間12万台のExpressサーバーをBTO(Build To Order)で生産しているNECプラットフォームズの甲府事業所をレポート。前編は工場の概要やボード製造の工程を見てきたが、後編はいよいよ装置の組み立て工程に入っていく。およそ10万通りのサーバーを良品として作り続けるための工夫を間近で見てきた。
最短4日納品!しかも遵守率100%をキープ
ボード製造の次は、ボードや電源、メモリ、筐体などを組み付ける装置組み立て工程に移る。Expressサーバー生産のポイントは、やはり顧客の要求仕様に応じて、1台ずつ生産するBTO(Build To Order)をいかに効率的に実現しているかだ。
実際、甲府事業所で生産される12万台のExpress5800サーバーのほとんどは、BTOの受注生産。およそ10万通りの個別仕様の中から、顧客の指定する構成で生産を実施する。つまり、ここで生産されるのは、すべて違うサーバーということになる。以前は基本ユニットとオプションが個別に配送され、それをお客様のもとで組み込んで動作検証しなければならなかったが、今はオプションの組み込みやOSのインストール、動作確認まで済ませた状態で届く。そのため、コンセントを入れればすぐ動き、設置や調整のトラブルもない。
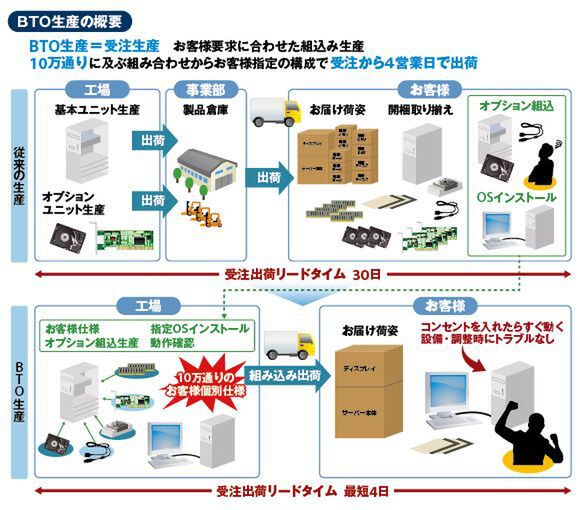
従来の生産とBTO生産の違い。納期や顧客の手間もまったく異なる
納期は、受注から最短4日。「最短4日と言ってますが、他の製品との品揃えに営業が1.5日、検査で8時間程度は費やすので、ものづくりしているのは実質1日~1.5日間です」(中西氏)とのことで、非常に短いリードタイムでの製造を実現。しかも現状100%の回答納期遵守を実現しているという。国内生産ならではの強みと言えるだろう。
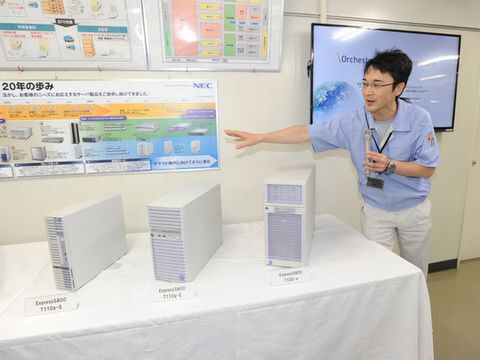
タワー型のExpress5800シリーズとNECプラットフォームズ 甲府生産統括部 装置製造部 シニアエキスパート 中西 孝征氏
10万通りのサーバーを間違いなく、確実な納期で生産すべく、社内では営業管理や物流管理、生産管理のシステム、そして現場の生産ライン管理システムが緊密に連携している。NECプラットフォームズ 執行役員 渡邉祐子氏は「最初は不要品を廃棄するところからカイゼンを始め、徐々に1ラインで複数のモノを作れるようにしました。そうした積み重ねにより、2~3倍工数が違う製品を同じラインで製造できるようにもなりました。今は良品を作り続けられるよう、管理された流れを構築しているところです」と語る。実際のラインを見ていこう。
ピッキングから部品のチェックまでRFIDをフル活用!
Expressサーバーを製造するのは工場棟の3階になる。マシンメインのSMT実装と人手を介したT/H実装という2つのラインを擁する1階に対して、3階はフロア全体が資材置き場、組み立てライン、検査という単一ラインとして構成されている。
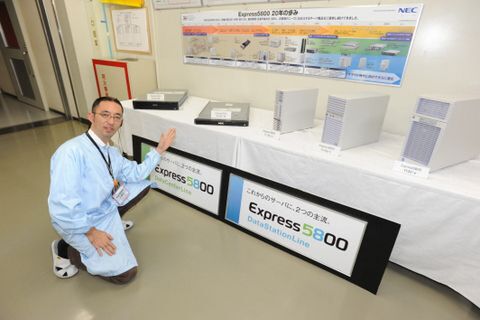
まさにExpress5800シリーズの故郷でもある工場3階の入り口に実機を展示
当日製造する台数は、前日の受注情報を元にして夜中に確定する。受注情報を元に発行された「生産指示かんばん」を各ラインの掲示板に立てるところから製造はスタート。オペレーターが顧客の仕様にあわせた資材をラインに供給し、オペレーターが組み立てを実施する。組み立てが完了した製品は自動で検査された後、最後に梱包と出荷準備が行なわれる。
数多くの資材から必要なものをピッキングし、およそ10万通りの構成で顧客の仕様に応じた製品を作るために、ここでもRFIDが大活躍している。顧客ごとの構成を含む注文情報は、生産指示かんばんより1台づつ発行されるトラベラーと呼ばれるRFIDに格納されている。オペレーターはトラベラーを元に資材のピッキング、作業内容の指示、使用部品情報の収集、構成の確認などを行なう。
たとえば、「買い物」と呼ばれる資材のピッキングではこのトラベラーのRFIDを読み取らせることで、必要な資材トレイのLEDが点灯するようになっている。トレイ前のインジケーターに表示される個数をピッキングし、ボタンを押すとピッキングは完了。取り漏らしがあると、グリーンランプがつかず、次の作業にも移れない。これなら必要な部品のみをラインに供給できるわけだ。
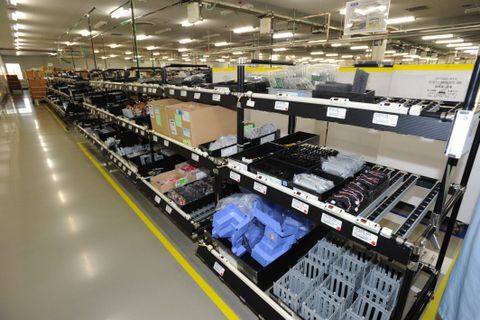
ずらりと並ぶ資材。必要とされる分だけプールされている
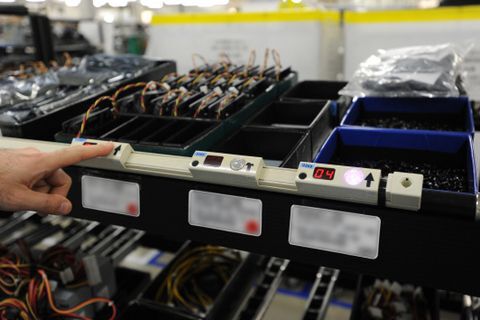
ピッキングする部品の前のLEDが点灯。表示個数をピックアップし、ボタンを押すと作業完了
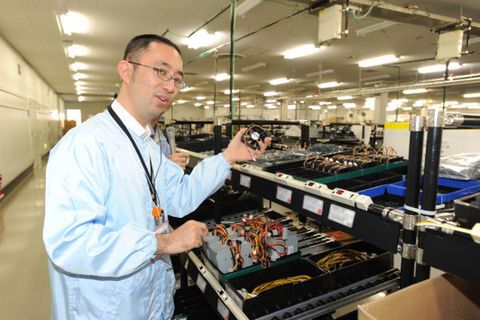
これなら必要な部品を必要な個数、ピックアップできます
「お客様からいただいた仕様を間違えないよう、RFIDを使って、5段階のチェックを行なっています。やりすぎじゃないかと言われることもありますが、このおかげで異なる仕様で送られてきたというおしかりを受けたことは過去に一度もありません」(中西氏)。
生産ラインは1階と同じリレー生産方式を採用しており、複数のオペレーターが作業範囲を固定せずに隣の作業を応援する。「毎回違うモノを作らなければならず、しかも生産数も内容も変わります。その一方で、品質やリードタイムは安定させなければなりません。こうした変動に対応すべく、ここでの作業はすべて人で行なっています」(中西氏)。顧客ごとに仕様が異なるため、作業指示はすべてモニターに表示され、部品も個別に供給される。
複数のオペレーターが作業を進めるリレー生産方式の場合、きちんと引き継ぎが行なわれるかが大きな鍵。その点、ここでは作業の途中であっても、「ネジを締める順番まで細かく作業手順が決められているので、進捗は一目で把握でき、引き継ぎもスムースに行なえます。むしろ、引き継ぐことで手順が守られているかの相互確認ができるんです」と語る。
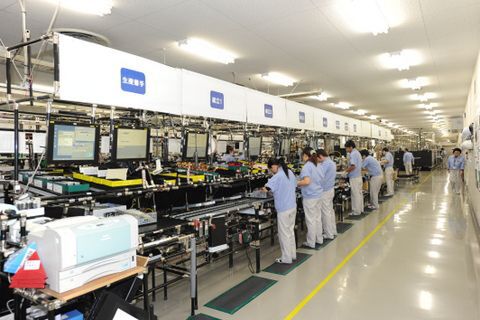
複数のオペレーターが連携して組み立てを行なうリレー方式を採用
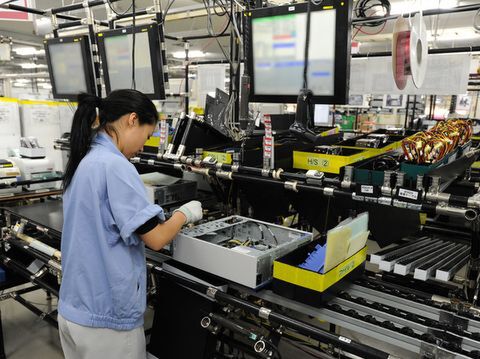
オペレーターの前面にあるモニターで作業手順を表示。顧客ごとの仕様にあわせた部品は黄色い箱で供給されている
こうして組み立てが終わった製品はいったんラインの外に出されて、検査工程に入る。ここでも顧客ごとの構成がRFIDで読み取られ、OSやソフトウェアを自動インストール。蓄積された品質ノウハウに基づき、お客様ごとの仕様に必要な機能試験やエージングなどの耐久試験が自動的に行なわれ、ようやく梱包という流れになる。
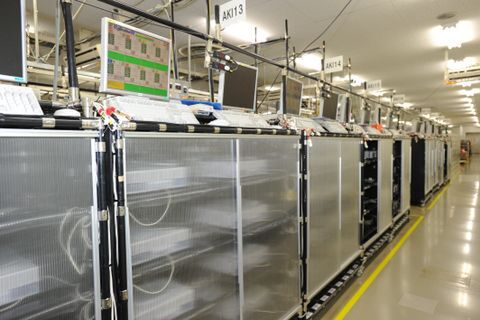
自動検査システムでは、さまざまな機能試験・耐久試験を全製品に対して実施
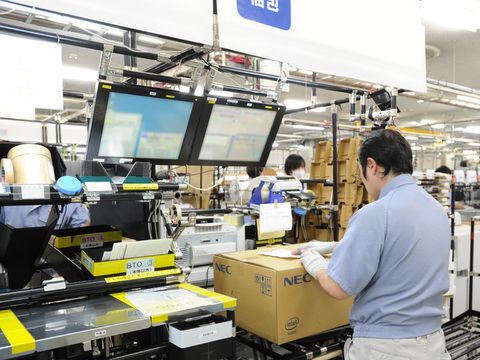
検査を経た後、ようやく梱包。同梱物に誤りがないよう、デジタルカメラで写真を撮った後に、梱包される
(次ページ、オペレーターの訓練はもちろん、設計段階から作りやすさを意識する)
