中国の蘇州工場の立ち上がりを見てきた二人
小池田氏や犬塚氏などと連携し、中国工場の製造現場で品質向上を進めているのが、音響生産企画部の刑部勝一氏と斉藤球紀氏だ。現在、ヤマハはRTX3500・RTX5000以外、2010年から普及価格帯のネットワーク機器はすべて中国の蘇州工場で内製化している。国内工場と同じ品質をどのように維持しているのか、お二方に聞いた。
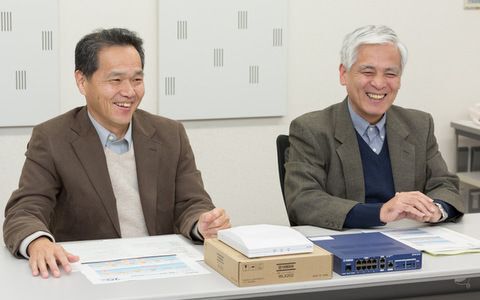
ヤマハ エレクトロニクス生産産統括部 音響生産企画部 主幹技師の刑部勝一氏、同 生産技術グループの斉藤球紀氏
お二人が所属する音響生産企画部は、生産拠点や開発、品質保証などとコミュニケーションをとりながら、新製品の立ちち上げに必要な開発⽇程や原価、生産準備などを管理する部門。おもにサウンドネットワーク、AV機器、PA機器をカバーしており、量産に入って以降も、品質をキープし続けるための監視・改善などを行なう。
このうち刑部氏は海外生産を始めた2009年頃まで開発部に所属しており、その後音響生産企画部でサウンドネットワークの製品を担当。2002年に設立した中国の蘇州工場と生産計画を調整する工場にある。一方、斉藤氏は刑部氏と同じ音響生産企画部の中にありながら、AV機器系の出身。中国の蘇州工場に2010年6月から赴任し、4年間現地の責任者を担当した。赴任して半年後の10月にネットワーク機器の中国での生産が始まったので、中国での立ち上がりを見てきた当事者と言える。
AV機器と同等、それより上の品質基準を確保
2人が担当している新製品の生産導入はまず「工程設計」からスタートする。製品をできるだけ簡単に、短期間で、しかもよい品質で安く作れるかを考え、プロセス化していく。製造部門との折衝でプロセスの検証が完了して初めて設備や治具などのリソースが手配され、本生産がスタートする。
そして、いったん生産がスタートすると、営業からの受注を受け、工場側で生産計画を作る。たとえば3月に1万台欲しいというリクエストを受けたら、工場側で人と部材と設備を確保し、あとは実際に組み立ての工程に移る。IT機器の場合、品質に関しては基板工程の安定が重要な要素のため、完全に内製化している。外装に関しても鈑金以外は内製を基本としているという。
製造現場のこだわりとしては、サプライチェーンも含めた品質管理の徹底が挙げられる。特に問題になりやすいコネクタなどは、重点的に受け入れ検査を行なうことで、高い品質を維持している。また、ネットワーク機器がAV機器と同じ外観基準を持っているのも特徴。「AV機器の場合、外観にひけや傷があるとすぐにクレームにつながります。こうしたAV機器と同じ品質をネットワーク機器側にも適用しています」(刑部氏)。IT機器では後回しになりがちな外観に関しても、きちんとクオリティを確保しているのが、まさにこだわりと言える。
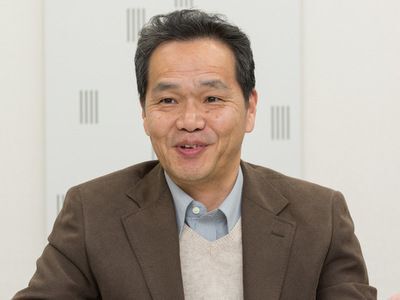
ヤマハ エレクトロニクス生産統括部 音響生産企画部 主幹技師 刑部勝一氏
そして、基板製造に関しては、AV機器よりも高い基準で品質を確保しているという。「たとえば、ハンダボールの大きさや数の管理基準が全然違います。ネットワーク機器に関しては、ヤマハ製品の品質基準としては異例の高さで特別にやってもらっています」と刑部氏は語る。
中国でも国内生産に負けない品質
製造現場では、製造キャパシティ、品質、コスト、納期などさまざまなパラメーターがあり、どれを優先するかはその企業によって異なる。その点、ヤマハは品質最優先の方針を掲げている。「中国⽣産になったから品質が落ちた」は許されない、ある意味過剰なまでに品質を意識した製造ラインの立ち上げをやってきたという。
斉藤氏は、「ひょっとしたら、不良が混じったかもしれないという段階でラインをストップし、点検・確認します。費用対効果を考えると割に合わないかもしれないが、それは別の話。最優先判断基準は品質です。費用・時間がかかってもこれらは後から補えますが、品質は後から補えず結果として総合的な損失は大きい。」と断言する。品質は信頼に、そして信頼がユーザーに直結する。特にネットワーク機器の場合は、納品された製品を直接ユーザーが使うため、とにかく不良を出さないことに専念したという。
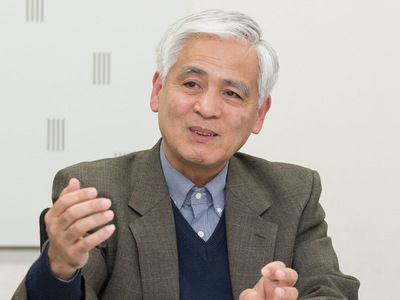
ヤマハ エレクトロニクス 生産統括部 音響生産企画部 生産技術グループ 斉藤球紀氏
とはいえ、実際に国内と海外の⼯場で同じ製造品質をキープするのは至難の業だ。たとえば、国内工場では設計仕様・品質ポイントは直接&的確に指示できるし、図面の細部まで記載しなくても工場側で判断・カバーできるが、海外工場では現実難しい。「日本と海外の工場の差は歴然としている。個体差もあるし、なにより日本では絶対的な経験がある」と斉藤氏は指摘する。
こうしたギャップを埋めたのは、日本と中国の強力なスタッフが力を結集したこと。日本から足繁くスタッフが現地に通い、金型メーカーやサプライヤーまで巻き込んで、品質向上に取り組んだ。「経験差・実力差があることを確認・理解しつつ設計仕様や要求品質を明確にし、実力差・経験差を埋める事や問題発生の予知・予防を行なうことに注力したのがよかったのかもしれない」と斉藤氏は語る。
たとえば、日本では“あうんの呼吸”で補われていた図面も、海外で製造するに当たっては、より詳細なものが必要だった。「こんな図面じゃ作れないと、斉藤さんからは何度もおしかりを受けました(笑)」(刑部氏)と語ると、「日本と同じようにやったら絶対に失敗する。そもそも背景が違うので、ギャップを埋めるような図面なり、道具なりがないとダメだと、刑部さんや担当の方には強く言ったかもしれません(笑)」と斉藤氏は応じる。マレーシアなどでの駐在経験のある斉藤氏は、海外と日本とのギャップを肌で感じととっており、その経験が中国でもまさに活きた形だ。
1ヶ月前でも弾力的な対応ができるように
デリバリに際しても、蘇州工場でチャレンジを行なっている。当時、従来から生産していたAV機器は3ヶ月前に生産台数が確定するのが基準で、納期も日単位の指定。製造の順番も、あくまで工場の都合で決められ、基本的には営業からの月内での優先度を対応するという概念自体がなかったという。
一方で、ユーザーの受注をベースに生産するネットワーク機器の場合は、生産計画の確定から納期までが約1ヶ月と短く、しかもオーダーの台数や機種がころころ変わる。さらにIT機器の場合、納期が日単位で指定される。「最初、聞いた時はなに言ってるの?という感じでした。AV機器がそうやっているんだから、こちらに合わせろというのが当初の意見でした」と斉藤氏は振り返る。
しかし、ネットワーク機器関係者と話していると、3ヶ月前に生産台数を決めてくれというのは難しいのがわかった。そこで蘇州工場ではネットワーク機器に関しては、1ヶ月前に弾力的に対応できるようフォーメーションを変更。出荷に関しても日単位で対応できるようにしたという。「開発の現場にいた時は、最初は納期に間に合うか心配でした」という刑部氏だが、実績を重ね続けて今に至っている。
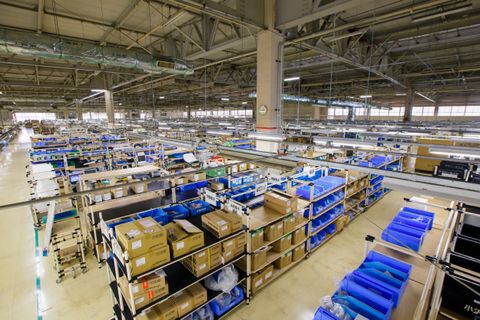
豊岡工場の組み立てラインの全景
「とにかく壊れない」と言われるヤマハのネットワーク機器。その高いい品質はスタッフの不断の努力から作られている。そして、それを支えるのがユーザーの声。開発部や品質保証、製造現場はもちろん、営業やカスタマーサービス、そしてその先にいるユーザーまでが1つのサプライチェーンに組み込まれ、ヤマハのネットワーク機器の品質を担保しているわけだ。
(提供:ヤマハ)
