40年前から無人搬送機が動いている工場
各地域でトップシェアを獲得している同社の強みは自社生産の高い品質。ものづくりにかけては2つの思想をかかげています。
1つは「五設一体思想」。マーケット調査に始まり、商品設計や工法、設備・金型、工程管理など5つの部門が連携することで製品の品質を高め、開発期間を短縮することをめざします。
もう1つは「一貫内製化」。金型から部品づくり、組み立てまですべてを内製。「良い商品は良い部品から。良い部品は良い金型から」を旨として技術者育成にも力を入れているそうです。
ショールームには同社で作ったというお弁当箱のような金型のサンプルがあり、フタ部分がなめらかに動きました。10μm単位の精度ですり合わせしたというもので、技量が伺えます。
ものづくり思想は昔から変わっていませんが、最近ではIoTシステムを導入し、生産プロセスの見える化を推進中。データを把握することで、設備の稼働率最適化や、金型保全作業の効率化などにつなげているということです。
ということで、実際に配線器具を作っている工場を見せてもらいました。
工場は4階建て。1階と3階で金属プレス加工、4階でプラスチック成形加工、2階で組み立て・検査・梱包という流れになっています。
最初に見たのは金属プレス加工。1個あたり最速0.04秒という驚異的な高速生産で、「ガッチャン、ガッチャン」ではなく「ガガガガガッ」というプレス音に驚かされました。
次に見たのはプラスチック成形。面白かったのが熱硬化性樹脂の圧縮成形です。熱々の金型で樹脂を熱するという料理のような工程で、できたばかりの樹脂パーツには餃子の羽根のようなバリが内外についています。この状態のパーツを機械に入れてガラガラ回すとアラ不思議、外側のバリが取れていきます。投射材を吹きつけることで内側のバリもきれいに取れました。欠けやすい材料でもきれいにバリ取りができるのは同社独自のノウハウがあるということでした。
そしてもっとも感心したのは次に見た組立工程です。各階で生産されたパーツが無人搬送システムでラインに供給されていきます。天井と地上それぞれにドローン的な無人機が動いているのを「ハイテクですなあ」と思いながら見ていたのですが、基本的なシステムが作られたのはなんと約40年前。私が生まれたころから無人化が進んでいたということに驚かされました。
もうひとつ感心したのが、1工程1チェックという検査体制。きちんと組み立てられているかを組み立て工程1つごとにチェックしているんですね。パネルの見た目を検査する外観検査、スイッチを押したときの押し心地が狙いどおりになっているか検査する感触検査などもあり、「そんなところまで」と驚かされました。
最近ではAIを使った外観検査精度の向上にも取り組んでいるということ。最終工程にはロボットの姿もあり、現在はまだ人が関わる工程がありますが、今後はさらなる自動化・効率化が進んでいきそうです。
スイッチを見る目が変わった
パナソニック エレクトリックワークス社 配線器具マザー工場の津工場で、スイッチやコンセント生産現場を見てきました。生産の裏側に見えたのは高い品質へのこだわりです。日常的に使われている配線器具は安心・安全が最優先。そのため金型から自社生産にこだわり、組み立てでは1工程1検査という厳しい検査を経て作られているということを初めて知りました。これまでは特に何も気にせずパチパチ使っていたスイッチやコンセントですが、ちょっと見る目が変わってきますね。
書いた人──盛田 諒(Ryo Morita)
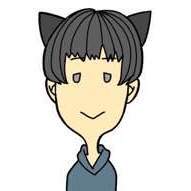
1983年生まれ。5歳児と1歳児の保護者です。Facebookでおたより募集中。
人気の記事:
「谷川俊太郎さん オタクな素顔」「爆売れ高級トースターで“アップルの呪縛”解けた」「常識破りの成功 映画館に革命を」「小さな胸、折れない心 feastハヤカワ五味」
アスキーキッズメルマガ 毎週土曜に配信中
アスキーキッズは毎週土曜、一週間ぶんの記事をまとめて読めるメールマガジンを配信中。人気連載「ほぼほぼ育児」をはじめ、ニュース、イベント、プログラミング教育入門、みんなの子育て体験談など、子育ての参考になる情報満載です。ご登録はこちらから。
