
本記事はソラコムが提供する「SORACOM公式ブログ」に掲載された「見える化、監視の次は? ソラコムが考える製造業IoTのメリットと課題」を再編集したものです。
目次
求められるのは一貫して「可視化」 でもPLCはデータ活用前提ではないPLCのデータ取得を妨げる課題感とセンサーの必要性
外に出せない、ラインがつながらない 少量多品種でデータがとれない
可視化とデータ活用はつながっていそうで、実はつながっていない
デジタル化のコストが大きい だからこそスモールスタートしやすく
製造業はモノを作っているだけじゃない
製造業が柔軟性を得るためのデジタル化、そしてIoT+AIによる価値創造へ
本記事は、ASCII.jp(株式会社角川アスキー総合研究所)に掲載された記事より転載/再編集したものです。
元記事:https://ascii.jp/elem/000/004/183/4183835/ 文:大谷イビサ 写真:曽根田元
IoTプラットフォームを手がけるソラコムが長らくフォーカスしている業界として製造業がある。工場でのIoT化はどうやって実現するのか? モノづくりの現場でなぜIoTが必要なのか? IoTがもたらすメリットと課題とは? 製造業での経験を持つソラコム ソリューションアーキテクトの井出尭夫氏とソラコム エバンジェリストの松下享平氏に話を聞いた(インタビュアー ASCII編集部 大谷イビサ 以下、敬称略)
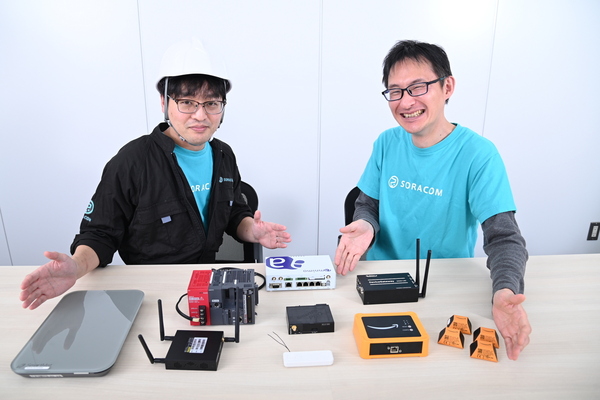
求められるのは一貫して「可視化」 でもPLCはデータ活用前提ではない
大谷:まずは製造業IoTというジャンルで、ソラコムが手がけてきたソリューションについて聞かせてください。
松下:ずばり可視化です。われわれもIoTに7~8年くらい取り組んできましたが、製造業における「今見えていない情報を見てみたい」という可視化のリクエストは、継続的にあります。
たとえば、生産ラインが止まってしまった場合、止まってしまった事実は確認できていて、なぜ止まったのかを知りたいということがあります。でも、データ自体はPLC(Programmable Logic Controller)で取得できるので、これをクラウドに送信すれば可視化は可能です。PLC内にログとして残っていても、リアルタイムでチェックできず、活用されていないという状態です。
大谷:製造業にあまり馴染みがないのですが、PLCとはなんでしょうか?
井出:製造現場の機械は、PLCというコントローラーで操作します。PLCは基本コンピューターなので、プログラムに従って機械を動かします。機械との間はさまざまな形式で接続されており、制御信号と応答信号が行き来しています。
松下:もしPLCがない場合は、人間が手動でボタン操作するイメージになります。プレス機なら、人がボタンをポチッと押して、上げたり、下げたりします。
井出:でも、PLCがあれば、この作業をプログラムに従って操作してくれます。センサーで高さを検知して、「これくらいの高さからプレスする」という指示も可能です。従来、人間が目視でやっていたことが、PLCならプログラムで自動化できます。
機械の横にある制御盤にはだいたいこのPLCが収納されています。だから、機械からの信号はすべてPLCに送られてくるわけで、データが欲しければPLCから取得すればよいという話になるわけです。
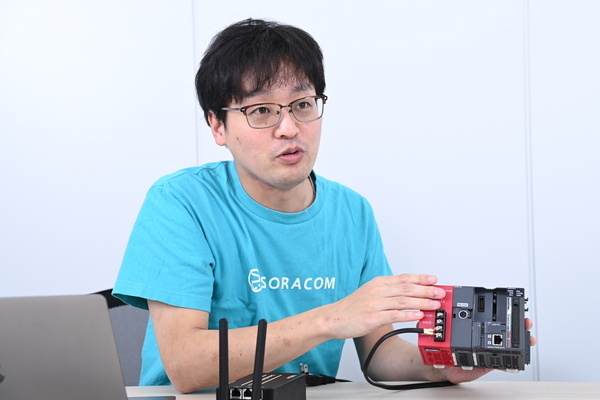
松下:工場におけるFA(Factory Automation)で生産設備を自動化するための装置としては、十中八九このPLCの話になります。だからこそ、製造業の業務効率化や作業品質向上を考えるとき、PLCからのデータ取得と活用が論点になります。
大谷:このPLCは、データ活用をする前提で利用されているものなんですか?
松下:私の見解では、データ活用が前提ではないと思います。元々、機器を高速かつ精密に操作するコントローラー(制御装置)として作られたものなので、データを長期保持するためにストレージを持っているとか、データ出力を前提としているわけではないんです。そういった機能は後付けするものになります。
PLCのデータ取得を妨げる課題感とセンサーの必要性
大谷:なるほど。工場の見える化にはPLCとの連携が不可欠。でも、PLCはデータ活用を前提している訳ではないので、後付けが必要。どうやって後付けするのでしょうか?
井出:ちょっと角度を変えて、IoTがどのようにPLCのデータを取得しているか説明しますね。
ボックスに収められているPLCを操作するために、通常はボタンやタッチパネルを使います。すなわち、PLCには外部から操作できるインターフェイスやプロトコルがあります。PLCからデータを取得するのは、このインターフェイスやプロトコルを利用します。
具体的にはIoTゲートウェイという装置がPLCにコマンドを発して、返り値を得ることでデータを取得し、クラウド側に送ります。だから、デバイスゲートウェイはある意味プロトコル変換器と言えるかもしれません。
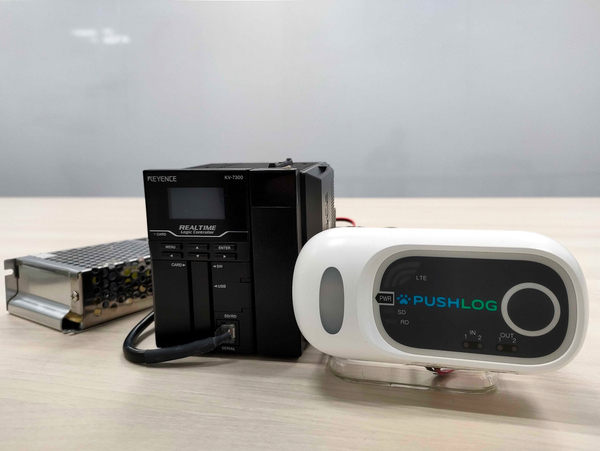
大谷:これはIoTという概念といっしょに生まれた装置なのですか?
井出:もともと製造現場の見える化に関しては、SCADA(スキャダ)という仕組みがあるのですが、これらはオンプレミス向けのものが多いのです。これがクラウドまで延伸したのが、製造業におけるIoTの1つの形です。
大谷:であれば、PLCのデータを取得し、SORACOMでクラウドに送信できる装置を設置すれば、クラウドで分析できるのですね。
井出:ただ、PLCには悩ましいところがあります。たとえば、何百度の高温となる熱処理炉とかも、このPLCで制御するんです。PLCはデータをとるための装置ではなく、あくまで制御するための装置なので。
でも、これがネットワークにつながることで、外部からの不正利用のリスクが高まります。極論すれば人命に関わるわけです。そのため時には、現場からは「PLCと得体の知れない装置を同居させるのはまかりならん」といった意見も出ます。
こういう場合は、PLCからデータを得るのではなく、直接センサーでデータをとります。例えば、LTEを搭載したセンサーを外付けすれば、PLCの構成やネットワークに影響なくデータを取得できます。
松下:そういう意味では、このAmazon Monitron(以下、Monitron)も外付け型センサーの類です。加速度センサーとバッテリー、BLEが搭載されているので、機械に取り付ければ、振動データを取得。デバイスゲートウェイを介して、データを送信して、AWS上で可視化できます。
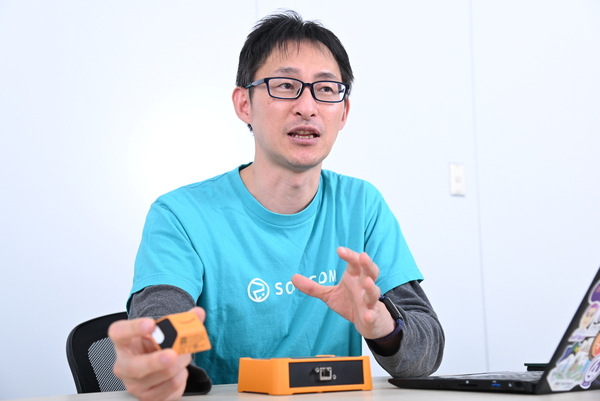
大谷:これは故障予知や障害検知が目的なんですかね。
松下:ポンプやベルトコンベヤーを動かすモーター等、 回転機構を持つ機械の場合、劣化すると振動が大きくなります。軸受けが摩耗ですり減ったりすると、すき間が大きくなるからです。そのため、振動音や間隔が大きくなったら、機械や部品交換になるのですが、これまでは人間が音を確認したり、触診するみたいなアナログな検査だったんです。
大谷:機械の不調を心の目で見るみたいな(笑)。
松下:そうですね。確かに機械から稼働状況のデジタルデータが直接得られたら一番いいんでしょうけど、先ほど話したようなPLCにつなげたくないとか、そもそもインターフェイスがないといった場合には、センサーを直接装着して、データを収集するというソリューションになります。
外に出せない、ラインがつながらない 少量多品種でデータがとれない
大谷:ここまでで可視化を前提とした製造業IoTをどうやって実現してきたかを見てきましたが、これまでにプロジェクトをこなす中で、現状の製造業IoTの課題ってどうお考えでしょうか?
松下:まず「データを外に出したくない」という意見は、製造業には長らくありますね。例えば単位あたりの生産データは、いわばその工場の実力値とも言えるので、外に出すことにセンシティブというのはよくわかりますが。
大谷:ここで言う「外」とはクラウドのことですか?
松下:イメージ的には「社外」ですかね。結果的にインターネットを通過させたくないとか、クラウドということかもしれませんけど。こういうセキュリティに関する懸念はどの製造業でもいまだに強いです。
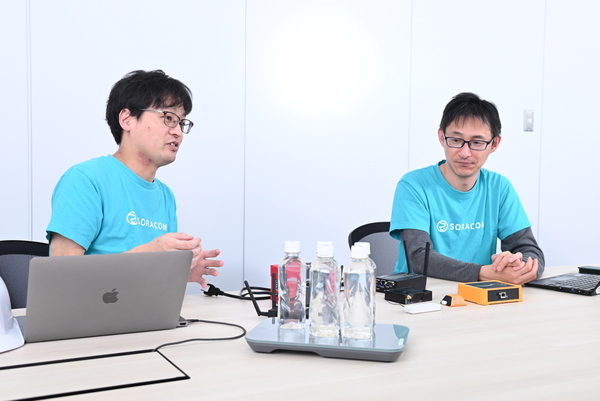
あと、ソラコムへのご相談をまとめてみると、現場でのデータ活用が遅れている気がするんですよ。製造業の現場って、FAという概念自体が以前から浸透しているので、工場では高価な機械が動いていて、データも容易にとれそうな気がします。生産数や歩留まりなど簡単に可視化できそうなんですが、そういうわけでもない。そこらへん、元製造業の井出さん、どうですかね?
井出:製造業も大別すると、半導体や電子デバイスのように、ほぼ完全に自動化されたライン生産の量産工場と、フライスで金属を削ったあとに、次のラインで加工して、次のラインで研磨してみたいな手作業のつなぎ合わせみたいな準量産・小ロット生産の工場に分けられます。
前者のようなライン生産の量産工場は、時間あたりの生産量がビジネスそのものなので、可視化や自動化が前提だと思います。大量生産前提なので、コストもかけられます。問題なのは後者の方で、ある加工機にPLCが取り付けられていて、データが出力されても、他のラインや機械と連携してない。
松下:前職でアセンブリの工程は見てきましたが、今から思えば、わりと職人技なんですよね。数字化しにくいし、量産というほどではない小ロットでの生産でした。生産依頼をして、ようやく使えそうなデータが取れたと思ったら、そのロットの生産が終わってしまうんですよね(笑)。製造業が少量多品種化したために、結果的にデータ活用が難しくなっているという側面はあると思います。
井出:そういう工場が多いだろうし、すべてデジタルにしていくのはけっこう大変です。
松下:以前、画像認識を用いて不良品を検知するというソリューションのために、不良品の画像を学習させようと思ったら、日本の製造業って優秀なので、不良品がなかなか出ないんです。不良品の画像がようやく集まったと思ったら、製造自体が終わってしまった(笑)。少量多品種がIoTやAIでのデータ活用を難しくしている要因の1つかもしれません。
可視化とデータ活用はつながっていそうで、実はつながっていない
大谷:なるほど。比較的中小規模の製造業では、手作業がけっこう多いために、ラインが分断されており、少量多品種の弊害でデータが取れないというのが、IT化の課題ということですかね。
井出:製造業の現場を見える化する目的ってなんだっけ? と考えると、製造業では、単位時間あたりの生産性を上げるために、どこに無駄があるか知ることが目的なんですよね。要はどこがダブついている時間なのか? 作れるのに作ってないのは、無駄なコストになります。見える化の効果は、その無駄を見ているのか、見ていないのかで、成否が分かれる気がします。無駄を見つけて、次のアクションにつなげないと価値は生まれないと思います。
松下:もう少し掘り下げると、たとえば経営指標として利益が増えたとか、必要な人員が減ったまでいくと、価値になります。逆にここまでやりきらないと、価値までは到達しません。「可視化」と「データ活用」って、一見するとつながっているのですが、実はつながっていないというのは、われわれが製造業のお客さまから得た学びだと思います。
大谷:なぜデータがビジネス上の価値につながらないんでしょう。
松下:見える化やデータによって、どのようなアクションをとるべきか。これを考えるのは、今のところ人間なんです。しかも、データサイエンティストのような専門家が見ないと、経営や利益にインパクトをもたらす具体的な行動に至らないんです。
本来ならば、このデータを見れば誰しもがわかるみたいなところまで行けたらいいのですが、データの解釈という部分までまだ足りてないのが実情です。たとえば、振動センサーのデータを見て、機械が大きく振動していることは見える化でわかっても、どうすればいいかのアクションにつながりにくい。これが見える化とデータ活用がつながっていない要因だと思っています。
デジタル化のコストが大きい だからこそスモールスタートしやすく
大谷:たとえば、農業IoTの場合、温度や湿度を計測することにより、なんらかのアクションにつなげています。過去に取材したSORACOM UGでのすいか栽培の事例は、ビニールトンネルの開閉や水やりの時期をIoTで見極めるようになったという話でした(関連記事:すいか栽培の温度管理や土壌測定にSORACOMを使ってみたら?)。製造業でアクションにつながりにくいのはなぜでしょうか?
松下:製造業では「とりうるアクションの選択肢が多すぎる」のかもしれません。農業の場合、収穫するとか、水をやるとか、アクションがあまり多くない。だから、データから導き出されるアクションがある程度決まってくるような気がします。
井出:製造業って、ガントチャートで管理するように、工程が複雑に入り組んでいます。だから、ボトルネックが生じている工程でない限り、一工程を最適化しても、全体のパフォーマンスにはあまり影響がない。製造業のカイゼンで一番難しいのはここです。個別最適を追求しても、全体最適につながらない。トータルのリードタイムを短くする施策をいかに組んでいくかが重要なんです。
大谷:そうなると、IoTだけで解消できる問題ではないということですね。理想的には、製造業の工程管理をトータルでコンサルティングして、その中でデータを収集したり、データを活かす方法を考える立場のパートナーが必要なのかもしれません。
井出:あとは、工程を最適化するために、ラインを変えられる権限を持った担当がお客さまの中にきちんといることですね。
大谷:なかなか一筋縄ではいかないんですね。
松下:現状、デジタル化のためのコストの方が大きくて、生産で得られる利益でまかなえない。つまり、投資額に対して、得られるメリットがまだ大きくないというのが、製造業IoTの根本的な課題です。
現状、FA機器をデジタル化するにも、追加の投資が不可欠です。しかし、コストがかかるからデジタル化をあきらめるというのは避けたい。そこに対してのわれわれの方法論が、今あるPLCを流用できるとか、既存の設備に後付けできるとか、とにかくコストを極力抑えつつ、できることをなるべく増やしていこうというものです。
大谷:スモールスタートしやすくするということですね。
製造業はモノを作っているだけじゃない
大谷:ここまでは工場の可視化により、機械の故障を予兆したり、検知したりといった話ですが、ほかのソリューションはありますか?
井出:顧客向けのリモート管理サービスとしてのIoTですね。
製造業がやっているのって、モノづくりだけではありません。製造業のDXを考えると、コストを削減することだけじゃなく、利益を上げていくこと。要は付加価値を上げていくことが重要になります。
今までの製造業ってモノ作って、売ったらおしまいでした。でも、デジタルやコネクテッドの導入で変わってきたのは、モノを売って、納めた後のサブスクリプション型サービスが実現するようになってきたことです。通信を使うことで、メンテナンスサービスを提供したり、モノが壊れたときにPLCからより詳細に分析するためのデータを取り出すこともできます。
松下:プラントなどに設置するバルブを製造するキッツという会社では、バルブの開け閉めの稼働データをとって、AIで解析しています。お客さまに対しては、月1回のレポートを提出し、メンテナンス時期をアナウンスするサービスとして提供しています。
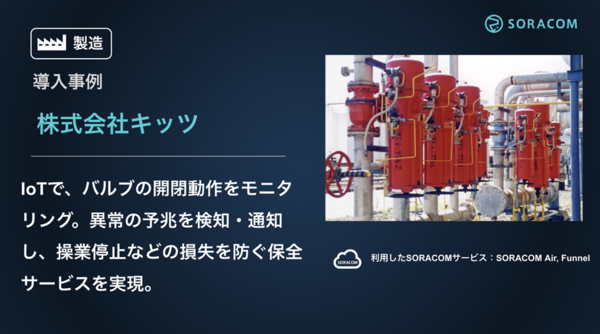
大谷:リモートでメンテナンスや障害の原因特定が可能になるということですね。この場合は、顧客のネットワークを使わせてもらうことになるのですか?
井出:顧客のネットワークとは別のネットワークをSORACOMのIoT向けデータ通信で構築した方が、ハードルが低いです。工場にあるOTネットワークって、コンピューターが使うITのネットワークと基本的には分離されていて、インターネットにつながらない閉域網になっていることが多い。ですから、メンテナンス用に別のネットワークを引くことになります。
大谷:なるほど。リモートサービスはいろいろ考えられますね。先日取材した京都のFUKUDAさんの事例と同じですよね(関連記事:残量検知デバイスでエンジンオイル販売を変えたFUKUDAとSORACOM)。燃料の在庫を適正化しつつ、顧客側の発注という作業自体をなくすという。
井出:製造で使う資材の在庫管理をIoTで効率化するという事例もあります。スマートショッピングでは、在庫管理ソリューションとしてスマートマットを提供していて、資材の重さを量って在庫管理し、足りなくなったら発注するという作業を自動化します。このスマートマットにも、SORACOMが搭載されています。
松下:在庫管理はどの業界でもあるのですが、物流業界以外には在庫管理の専任担当がいるわけではなく、他の業務担当が片手間に実施することも少なくありません。スマートマットを利用して、面倒な作業を自動化することで、本来の業務に集中できるという便利さがあります。
井出:これは比較的IoTでメリットが出やすいソリューションです。結局、資材が足りなければ製造に影響が出ますが、在庫を抱えすぎるとコストがかかるので、適正在庫を保つことが必要になります。
松下:AGCでは、タンクの残量検知を行なって、なくなる前に自動発注するシステムを構築しています。
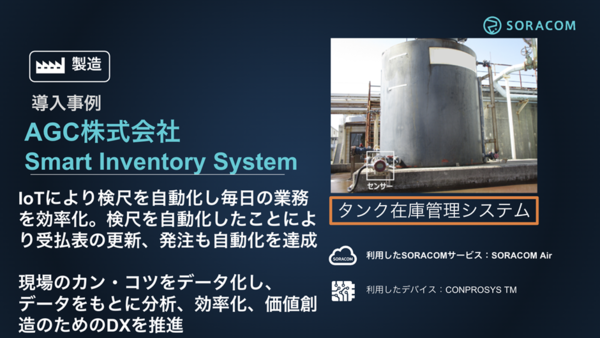
製造業が柔軟性を得るためのデジタル化、そしてIoT+AIによる価値創造へ
大谷:今後、製造業はますますデジタル化していくのでしょうか?
井出:製造業では、親会社、子会社、外部ベンダーなどが連携してモノづくりを行なっているので、上流の会社がデジタル化していったら、子会社や外部ベンダーはおのずとデジタル化を求められてくるはずです。
昨年のモノづくり白書をひもとくと、「サプライチェーンが分断されている」という課題が書かれています。今、作っているモノを、どのメーカーも恒久的に作ればOKという時代は終わっており、市場のニーズに合ったモノを作るために、発注先をダイナミックに選んでいく柔軟性が必要とされています。
松下:テスラモーターズとか、まさに好例ですよね。
井出:そのような判断を的確に行うために、デジタルを導入することで、サプライチェーンを管理したいというニーズが大きくなると思います。逆に言えば、デジタルがなければ、サプライチェーンの効率的な管理はできないはずです。
大谷:最後にAIの活用について教えてください。IoTで集めたデータをどのように解析するかという点で、いろいろ興味深いです。
井出:クラウドにはセンサーデータが溜まっているので、機械学習で正常、異常を解析するというのがオーソドックスなユースケースですね。
前述したAmazon MonitronにはAWSの機械学習アルゴリズムが組み込まれているので、デバイスからアプリまでワンストップで利用できるのが最大のメリットです。振動自体を可視化する製品は今までもありましたが、数が増えると監視も大変です。でもMonitronでは、数多くの機械の中から、どの機械を優先して部品交換した方がよいかまで教えてくれます。
松下:画像解析に関しては、先ほども話したとおり、データが溜まる前に製造が終わってしまうというプロジェクトが多いのが難点でした。一方で、生成AIに関しては、自社データをきちんと学習させることで、ナビゲートとして期待できるのではないかと思います。たとえば、故障時にどのように対応すべきか、自ら探さなくても、ガイドしてくれるみたいなイメージですね。
昨年末に参加したAWS re:Invent 2023のインダストリアルゾーンで見たデモは、工場のデジタルツインで機械の故障をアラートで上げてくれるというもの。これだけなら、まあ予想が付くのですが、さらにAWSの生成AIアシスタントサービス「Amazon Q」と組み合わせることで、故障した部品の品番と対応方法までアナウンスしてくれるんです。どの現場に行き、どの機械のどれをいじればいいかまで教えてくれる。これなら僕でもできるなと。
井出:マニュアルの「こんなときどうする?」みたいな例を、すべて把握しているということですよね。
松下:生成AIの精度を向上させる手法として「RAG(Retrieval Augmented Generation)」が注目されています。自社が持つデータやドキュメントと生成AIを組み合わせることで、例えば初期対応をどうすればいいかくらいはできそう。誰しも扱える製造ラインの実現にCopilotとして寄与できるのではないかと。無人まではいかなくとも、省力化にはつながるかなと思いますね。
大谷:ありがとうございました!
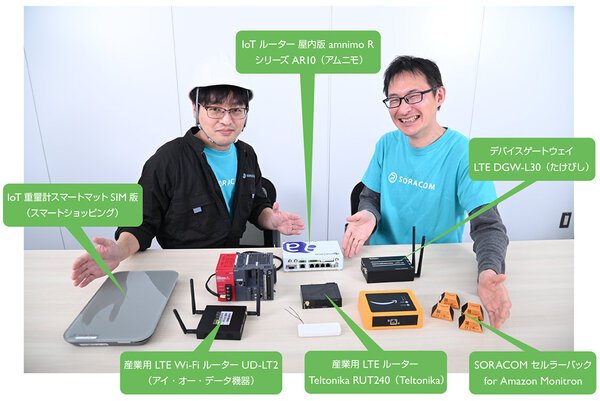
投稿 見える化、監視の次は? ソラコムが考える製造業IoTのメリットと課題 は SORACOM公式ブログ に最初に表示されました。
この連載の記事
-
第401回
デジタル
IoTの基礎知識から実務を網羅した一冊「IoTの知識地図」 ― 見どころ解説 -
第400回
デジタル
USB型LTEデバイス「Soracom Onyx」向け、防水・防塵アンテナセットの販売開始 -
第399回
デジタル
クラウド型カメラの新たな使い方を提案!ソラカメの新機能「ライブ視聴見放題」ご紹介 -
第397回
デジタル
Make a Global Impact as a Technical Writer at Soracom -
第396回
デジタル
SORACOM LTE-M Button powered by AWSの移行受付を開始、SPSアワード 2023の表彰を発表 takuyaのほぼ週刊ソラコム 04/01-04/14 -
第395回
デジタル
SORACOMの新機能開発の舞台裏 ― お客様の声からリリースまでの道のり -
第394回
デジタル
動画で分かる!SORACOM Lagoon 3への移行の手順 -
第393回
デジタル
ソラカメ運用管理をより簡単に!アクセス権限設定テンプレートのご紹介 -
第392回
デジタル
生成AIによる「ブログの原稿作り」手順やプロンプトを公開 -
第391回
デジタル
クラウド型カメラの実機を見ながら相談できる「ソラカメ デモルーム」