製造業×IoTはもはや実践段階、一方で製造業とITベンダーとの意識差という課題も
日本の製造業はIoTで強くなれるか?「MCFrame Day 2016」レポート
2016年03月01日 09時00分更新
2月19日、“日本の製造業とIT”をテーマとした東洋ビジネスエンジニアリング(B-EN-G)のプライベートイベント「MCFrame Day 2016」が東京・虎ノ門ヒルズフォーラムで開催された。IoTによる生産性向上やビジネス変革も喧伝される中で、製造業にとっての現実的な解はどこにあるのか、幅広い視点から議論が交わされた。
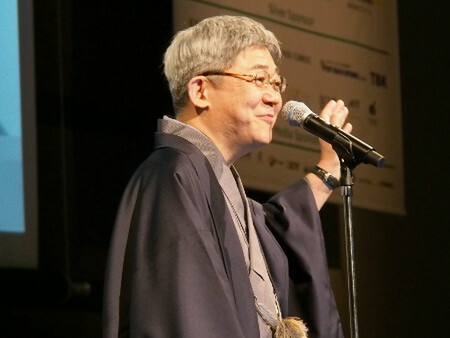
「日本の製造業、ものづくり」を意識して和服姿で登壇した、東洋ビジネスエンジニアリング 代表取締役社長の大澤正典氏
今年で10回目を迎えたMCFrame Day。1000名を超える来場者でにぎわった今回のテーマは「ITと現場の真の融合」だ。
イベント冒頭、和服姿で挨拶に立った同社代表取締役社長の大澤正典氏は、製造業においても「IoTやビッグデータを活用した経営の効率化が、世界規模で進められている」と述べる。海外拠点も巻き込んだ経営のさらなるスピード化、IoTを通じた製造業ビジネスのサービス化といった新たな潮流にどう取り組んで行くかが、すでに概念検証段階を過ぎ、具体的な経営課題になっているのが現状である。
大澤氏は、エンジニアリング会社出身のB-EN-Gとして、従来提供してきたERPサービスに加えて、今後は製造業のIoT活用も強く支援していきたいと語った。B-EN-Gでは2月、AWS(アマゾンウェブサービス)のパートナープログラムへの加入しており、クラウドを活用した製造業向けIoTソリューションを広く展開していく方針を明らかにしている。
製造業、コンサルタント、ITベンダーの代表者が「製造業とIoT」を議論
続くオープニングセッションでは、その「製造業とIoT」をテーマとして、製造業、経営コンサルティング、ITベンダーそれぞれの代表がパネラーとして登壇し、現状と未来を見据えたディスカッションが交わされた。
(左から)日経BP 技術情報グループ 企画編集委員の三好敏氏(モデレーター)、アーサー・D・リトル シニアアドバイザー/日本工業大学技術経営大学院 教務委員長の清水弘氏、安川電機 代表取締役 専務執行役員 技術開発本部長の小笠原浩氏、シスコシステムズ シスココンサルティングサービス シニアパートナーの八子知礼氏、アマゾンウェブサービスジャパン(AWS) マーケティング本部 本部長の小島英揮氏、東洋ビジネスエンジニアリング 常務取締役、CMO/CTOの羽田雅一氏
ディスカッションのテーマは大きく2つ。「ITで日本の製造業は強くなれるのか」、そして「製造業の新しい時代に向けて取り組むべきこと」だ。
議論の中では「製造業側とITベンダー側での意識の違い」といった課題も浮き彫りになったが、各氏とも具体的な事例や提言を交えながら、日本の製造業がIoT、そしてITの活用でこれからどう変革を遂げていくべきかの道筋を示した。
IoT時代に実現する「デジタルな現地現物主義」とは
MCFrame Dayの最後を飾るクロージングキーノートでは、製造業向けのコンサルティングとソリューション提案を手がけるエイムネクストの清威人氏が登壇し、製造現場の生産性向上のための具体的なIoT活用について語った。
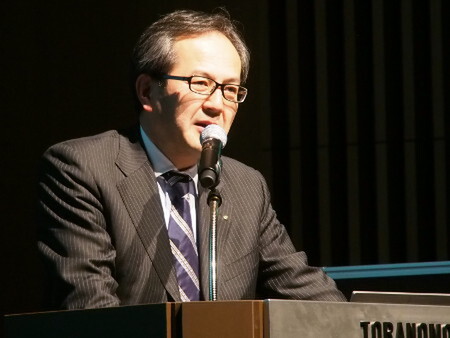
エイムネクスト 代表取締役の清威人氏
清氏は「日本の製造業企業の強みは『現地現物主義』だと思う」と語る。現地現物主義とは、机上に集まるデータだけで考えるのではなく、現地に赴いて現物を見ることで、たとえば周辺設備や前後の工程などの状況も含めて把握し、より正しい判断や実行、生産のあくなき“カイゼン”を目指すものだ。
そしてIoTの時代には、この現地現物をさらに発展させた「デジタルな現地現物主義」が実現できるのではないか、というのが清氏の問いかけである。
「従来の現地現物主義でも、たとえば顕微鏡や測定メーターで見なければわからないようなことなど、わからないことはまだまだあった。IoTを用いてこうしたデータを全部可視化していくことで、これまでの壁も突破できる」(清氏)
同社が2008年ごろから提唱、取り組んでいる「スマートファクトリー」では、生産設備、検査装置、入退室管理システム、作業者用端末などをネットワークを通じて統合し、あらゆるデータを収集、蓄積する。このデータはリアルタイムに処理、あるいは統計分析処理し、生産管理システムやERPなどとも連携可能にする。IoT時代になれば、さらに豊富なデータが活用可能になるはずだ。
こうした生産現場のデータ活用の仕組みを背景として、どのような生産性向上策が実践できるのか。清氏は「改善機会の発見と優先順位付け」「統計だけでなく個別データの可視化」「手作業/間接業務の削減」「キャッシュフローによる改善評価」「管理モデルの自動化」という5つのアイデアを紹介していった。
たとえば「改善機会の発見と優先順位付け」では、これまで計画数と実績数しか存在しなかった生産現場において、消費電力や総停止時間、作業者ごとの生産性といった幅広い視点からのデータも取り込むべきだという。これにより、原価低減や効率化のために本当に必要な取り組みを、優先順位を付けて実施していくことができるからだ。
また「手作業/間接業務の削減」については、基データはたった数十種類しかないにもかかわらず、必要な帳票をそれぞれの部門/担当者が個別に作成することで1000種類以上の帳票にも膨れあがっていた工場のケースを紹介。スマートファクトリー化によるデータの統合/共有と、必要なデータの自動取得を進めることで、無駄な間接業務を大幅に削減することができることを説明した。
まとめとして清氏は、スマートファクトリー導入を成功させるためのポイントを3つ挙げた。IoTやシステムを導入すれば万事解決ということはなく、それらのツールを活用して、生産管理の土台や組織の枠を超えた改善活動が実行できる組織こそが重要だと語る。
「さらに、自社のものづくりという大前提をふまえ『データにおぼれないこと』『ノウハウを流出させないこと』も大切。『デジタル化しない領域を残す』という判断があってもよい」「さらなる効果を得るためには、基幹システムとの連携を強化したり、設計と生産など部門を超えた業務連携に活用したりといったことが考えられる」(清氏)
* * *
オープニングからクロージングまで、多くの来場者が熱心に耳を傾けたMCFrame Day。IT/IoT活用で日本の製造業が本来持つ強みを加速する「ITと現場の真の融合」に向けて歩む、そのヒントがもたらされたのではないかと感じた。
